Assessing the Impact of Environmental Factors on Safety Protocols
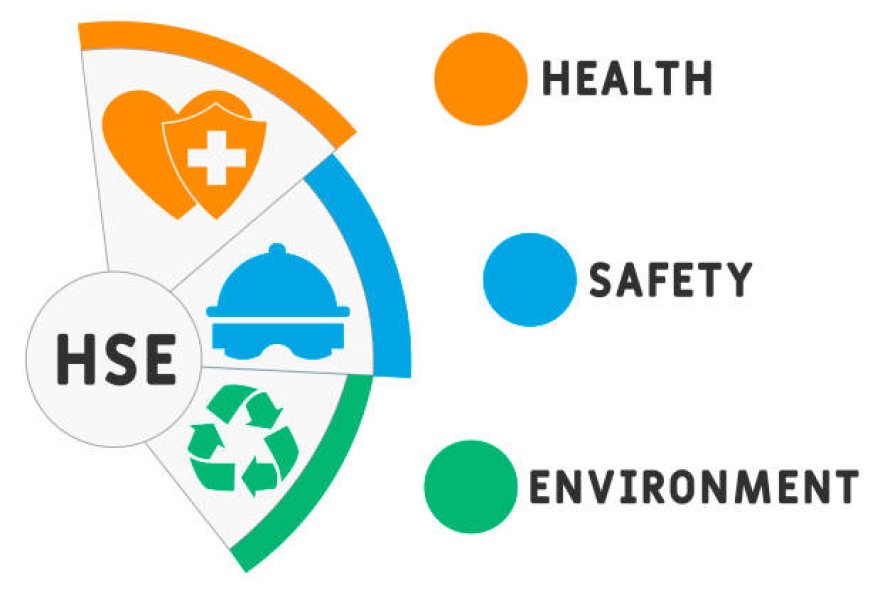
When it comes to safety, most people picture hard hats, caution signs, and emergency drills.
While these are all essential, there’s another major player in the game: the environment. Natural and man-made environmental factors can make or break safety protocols. Imagine a construction site in the middle of a heatwave or a factory dealing with air pollution—safety rules must adapt.
This article takes a deep dive into how environmental factors shape safety protocols, what organizations can do to stay ahead, and why ignoring these elements is a one-way ticket to disaster.
How Environmental Factors Shape Safety Protocols
A safety protocol is only as strong as the conditions it accounts for. Think about wearing gloves in extreme heat. Sounds smart until the gloves melt. Or, take icy roads. Standard traffic rules won’t cut it when nature decides to throw a frozen tantrum.
Organizations must adapt their safety measures to keep workers, the public, and assets protected. Let’s break this down into specific environmental factors that directly influence safety protocols.
1. Weather Conditions
Weather is one of the biggest influencers of safety measures. Rain, snow, extreme temperatures, and storms all introduce new risks.
-
Extreme Heat: High temperatures lead to dehydration, heat exhaustion, and heatstroke. Workplaces that involve physical labor, such as construction sites, need revised safety protocols during heatwaves. More frequent breaks, hydration stations, and adjusted work schedules help reduce risks.
-
Freezing Temperatures: Cold weather can cause frostbite, hypothermia, and increased risks of slips and falls. Outdoor workers, including those in transportation and agriculture, need proper insulation, heated shelters, and anti-slip footwear.
-
Storms and Heavy Rain: Electrical hazards, road safety concerns, and flooding risks spike when storms roll in. Companies need backup power systems, emergency evacuation plans, and weather-tracking tools to stay prepared.
Ignoring the weather is like forgetting sunscreen at the beach—things will get uncomfortable fast.
2. Air Quality and Pollution
Air pollution affects more than just the lungs; it influences workplace safety in surprising ways. Poor air quality, whether from industrial emissions, wildfires, or vehicle exhaust, can cause dizziness, respiratory issues, and long-term health effects.
-
Indoor Workspaces: Factories, warehouses, and office spaces must install air filtration systems to keep pollutants from affecting workers.
-
Outdoor Workspaces: Workers in cities with high pollution levels need protective masks and exposure limits to prevent health complications.
-
Hazardous Chemical Exposure: Laboratories, chemical plants, and construction sites require strict protocols for handling fumes, toxic dust, and airborne contaminants.
When the air quality drops, productivity follows. Nobody wants to work in an environment that makes breathing feel like a workout.
3. Natural Disasters and Geographical Risks
Some regions deal with unique environmental challenges that force safety protocols to level up.
-
Earthquakes: Workplaces in seismic zones must reinforce structures, secure heavy equipment, and conduct earthquake drills.
-
Flooding: Low-lying areas and coastal zones must plan for flood-resistant infrastructure, drainage systems, and emergency response procedures.
-
Wildfires: Regions prone to wildfires need evacuation plans, fire-resistant gear, and clear safety guidelines to minimize exposure risks.
The trick is to assume nature won’t take it easy. If an organization is waiting for a disaster to hit before taking action, it's already too late.
4. Noise Levels and Vibrations
Some industries, like construction, mining, and manufacturing, expose workers to dangerous noise levels and constant vibrations. Over time, these factors can cause hearing loss, stress, and equipment malfunctions.
-
Hearing Protection: Earplugs, noise-canceling headsets, and soundproofing measures reduce risks for workers in high-decibel environments.
-
Vibration Safety Measures: Anti-vibration gloves, properly maintained machinery, and limited exposure times prevent long-term damage.
Ignoring noise protection is like standing next to a jet engine for fun—it’s not going to end well.
5. Biological Hazards and Health Risks
Workplaces are not immune to biological threats. Whether it’s mold in an office, a viral outbreak, or exposure to hazardous bacteria, safety protocols must address these invisible dangers.
-
Healthcare and Labs: Strict hygiene measures, biohazard disposal systems, and PPE (Personal Protective Equipment) requirements keep workers safe.
-
Food Industry: Restaurants and food processing plants must maintain cleanliness to prevent contamination and foodborne illnesses.
-
Workplaces with Animal Exposure: Farms, zoos, and pet clinics must prepare for zoonotic diseases that jump from animals to humans.
A solid health and hygiene plan can mean the difference between a normal workday and a full-blown outbreak.
6. Chemical and Radiation Exposure
Industries working with chemicals or radiation, such as nuclear plants, medical facilities, and manufacturing sites, face a different set of challenges.
-
Handling Hazardous Materials: Strict guidelines for storing, transporting, and disposing of chemicals prevent exposure risks.
-
Radiation Safety Measures: Workers in nuclear facilities and X-ray labs must wear protective gear and limit their exposure.
-
Emergency Decontamination Plans: Organizations must train employees on how to respond to spills, leaks, or accidental exposure.
A single chemical mishap can turn a workplace into a disaster zone, so proper safety measures are non-negotiable.
Strengthening Safety Protocols Against Environmental Risks
It’s clear that environmental factors play a huge role in workplace safety, but what can organizations do to stay ahead?
1. Risk Assessments
Organizations must regularly assess environmental risks specific to their industry and location because what works in one place might be useless somewhere else. Just like the factors that affect I-130 processing time vary by case, workplace safety measures must be tailored to specific environmental conditions.
A warehouse in Arizona battles extreme heat, while a factory in Alaska worries about freezing temperatures and snowstorms. So a one-size-fits-all safety plan just doesn’t cut it. Businesses need to analyze their surroundings, identify potential hazards, and adapt safety measures accordingly before nature throws a curveball. If your safety protocol treats a desert like a tundra, you’ll either have overheated workers or very confused penguins.
2. Real-Time Monitoring and Technology
Gone are the days of guessing whether a storm is coming or hoping the air is safe to breathe. Smart technology does the heavy lifting now. Weather tracking systems, air quality monitors, and noise sensors provide real-time updates, allowing businesses to adjust their operations before conditions become hazardous.
The more data organizations have, the better they can make informed decisions rather than playing a dangerous game of "wait and see." After all, no one wants to be that company that ignored the warning signs and ended up on the evening news for all the wrong reasons.
3. Flexible Safety Policies
Rigid safety policies work about as well as a stiff umbrella in a hurricane—fine in perfect conditions, but useless when the unexpected happens. Environmental factors change constantly, and companies need adaptable safety measures that evolve with new risks.
Whether it’s adjusting work hours due to extreme heat, upgrading ventilation systems in polluted areas, or modifying evacuation plans for seasonal threats, businesses must stay flexible. Think of it like a seatbelt—you adjust it to fit, or it won’t do its job when you need it most.
4. Training and Awareness
A safety protocol is only as strong as the people who follow it, which is why proper training isn’t optional, it’s essential. Employees need to recognize risks, understand warning signs, and know exactly what to do when things go south.
Regular drills, workshops, and refresher courses keep teams sharp, preventing panic in real emergencies. After all, the last thing you want in a crisis is someone Googling “what to do during a chemical spill” while standing in the middle of one.
5. Emergency Response Plans
When disaster strikes, clear instructions can mean the difference between a well-organized evacuation and complete chaos. Every organization must have a documented emergency response plan that accounts for fires, floods, power outages, and anything else Mother Nature, or human error, might throw their way. Employees should not only know the plan but also practice it regularly so that reactions become second nature, not last-minute guesses. Because in an emergency, hesitation is about as useful as a parachute that comes with assembly instructions.
Furthermore, when safety lapses lead to injury, the aftermath can involve more than just medical bills—it can mean legal action. In such cases, consulting with a qualified injury lawyer ensures that workers understand their rights and receive fair compensation. Legal expertise can also guide companies in refining their protocols to prevent future incidents and reduce liability.
Conclusion
Environmental factors are not just background noise in the world of safety—they’re the main event. From extreme weather to air quality, noise pollution, and biological threats, these elements influence how businesses protect their people and operations.
Organizations that take these risks seriously build stronger, safer workplaces. Those that ignore them? Well, let’s just say nature doesn’t care about outdated safety manuals.
So, the next time someone complains about safety rules being too strict, remind them: better safe than sorry. Or better yet, better safe than stuck in a blizzard with no gloves.